The Industrial Internet of Things is the use of connected smart devices in industrial applications for purposes such as automation, remote monitoring and predictive maintenance. The IIoT is a more robust version of the Internet of Things, or IoT which is the realm of connected devices in commercial and consumer applications. In Industrial IoT use cases, smart devices may be deployed in construction vehicles, supply chain robotics, solar and wind power, agricultural sensor systems, smart irrigation, and more. These IIoT applications tend to have one thing in common: they are are deployed in challenging environments.
There are light industry IIoT use cases such as meters, and heavy industry use cases such as conveyors used in the mining industry, where devices can be subject to a wide range of environmental factors, from extreme heat and cold to moisture and vibration.
The Industrial Internet of Things is about deploying smart machines to capture and move data, sense changes in temperature, flow or volume, automate procedures for efficiency, accuracy and safety, deliver data into the right hands for analysis and decision making, and ensure that all of those processes happen on time, reliably and securely.
The IIoT and Worker Safety and Productivity
The use of smart devices has rapidly expanded, and today – with the enormous growth of the IoT and IIoT trends – it’s hard to find an industry that is untouched by this phenomenon. This leads to a few questions:
- Why are the IoT and IIoT expanding so rapidly?
- What does this mean for workers and jobs?
The answer to the first question is that the IoT and IIoT are responding to inefficiencies, lost revenue, and a need for organizations to work smarter, not harder. Automation can create unprecedented improvements and efficiencies that simply aren’t possible with a human workforce. This is not to say that humans aren’t necessary. On the contrary, engineers, application developers, data scientists and workers from every walk of life are needed to put these solutions in place and make use of them.
As a simple example, consider the farm worker who previously had to drive from one remote corner of acreage to the other to ensure watering systems or frost fans were turned on at the correct time. Today, that worker can check on systems from a laptop, ensure everything is working correctly and travel only to the location that actually needs servicing. If a center pivot irrigation system has rolled off course, for example, the worker can use GPS to quickly identify its location and then ensure that it is returned to the correct position. In other words, the Industrial Internet of Things is about improving efficiency and accuracy while reducing cost.
That leads to an answer to the second question. The impact of the IIoT on workers and jobs is that it makes them more efficient and improves productivity. It also reduces “busy work” and the likelihood of errors in tasks such as data logging, that are better handled by a smart device. Automated sensing and data gathering from dangerous and difficult-to-reach places even reduces risk to human lives. And it gets the right data to the right place for evaluation sooner. When an employee can get a smart phone alert that a tank is low or a piece of equipment needs maintenance, that improves the likelihood that problems can be solved early, before they become more expensive or catastrophic.
Examples of Industrial IoT Use Cases
One of the best ways to get insight into how commercial and industrial enterprises use IoT is through the many example IIoT applications. Let’s take a spin through a few of them.
Predictive Maintenance
Predictive maintenance applications seek to identify when a critical business process or piece of equipment is at risk of failure, so proactive and preventive maintenance can be scheduled to fix problems in advance and thwart downtime. Traditional methods can be very expensive and workers can inadvertently miss indicators that equipment is experiencing problems. In many cases, technicians and maintenance workers have traditionally had to travel to remote sites to perform manual checks, only to have to make another trip with a work order, replacement parts or batteries. Getting an alert that a problem is developing makes it possible troubleshoot and fix an issue with one truck roll, often before the end customer is even aware of the problem. The result is improved maintenance practices, reduced costs and enhanced customer satisfaction.
Here are a few examples of IIoT predictive maintenance applications across industries.
- Process monitoring – mining: In the classic game “Rock, Paper, Scissors” rock can be beaten by paper. However, in the real world, rock beats everything. In mining applications, large conveyor belts transport earth (lots of rocks) from one area to another over long distances, over a mile in some cases, where the material is processed to extract valuable minerals. If the conveyor belt and supporting equipment “go down” or stop, it can cost a mine millions of dollars in lost revenue. To ensure the conveyors work without interruption, 24/7, sensors are added to the conveyor to gather data points and send that data via a radio device (e.g. Digi XBee®) to a gateway and then to a remote monitoring application. Digi Remote Manager® can help monitor those gateways and devices at different mines and quarries to prevent undesired down time.
- Equipment maintenance – elevators: An elevator company wants to ensure that the customers who install their product receive the highest quality service. Rather than wait until a problem occurs that impacts daily operations and customer satisfaction, the company puts sensors in place, in hundreds of thousands of installed elevators. These sensors communicate data points through a gateway to a cloud environment that provides insights and automated notifications to field technicians.
- Asset monitoring – construction: An energy management company provides solutions to customers such as construction companies. They develop a range of IoT tools to help these organizations ensure they are optimizing vehicle use and identifying problems before they result in lost revenue. To predict hydraulic hose failure before it results in equipment breakdown, expensive hydraulic fluid cleanup and potentially injuries, the company develops a connected solution that monitors equipment, identifies and reports on data points that indicate a potential failure, and enables customers to set up alert conditions and receive automated notifications.
Predictive Maintenance Application Example
In the following predictive maintenance example, a radio module collects data from equipment in a grain elevator and sends it to an industrial router, which then delivers that data to cloud-based applications for visibility and further processing. If the data indicate certain conditions, a technician can see that in online application, or receive alerts from an application such as Digi Remote Manager®. The technician can workthrough a troubleshooting process remotely or send personnel to the site to perform the required maintenance.
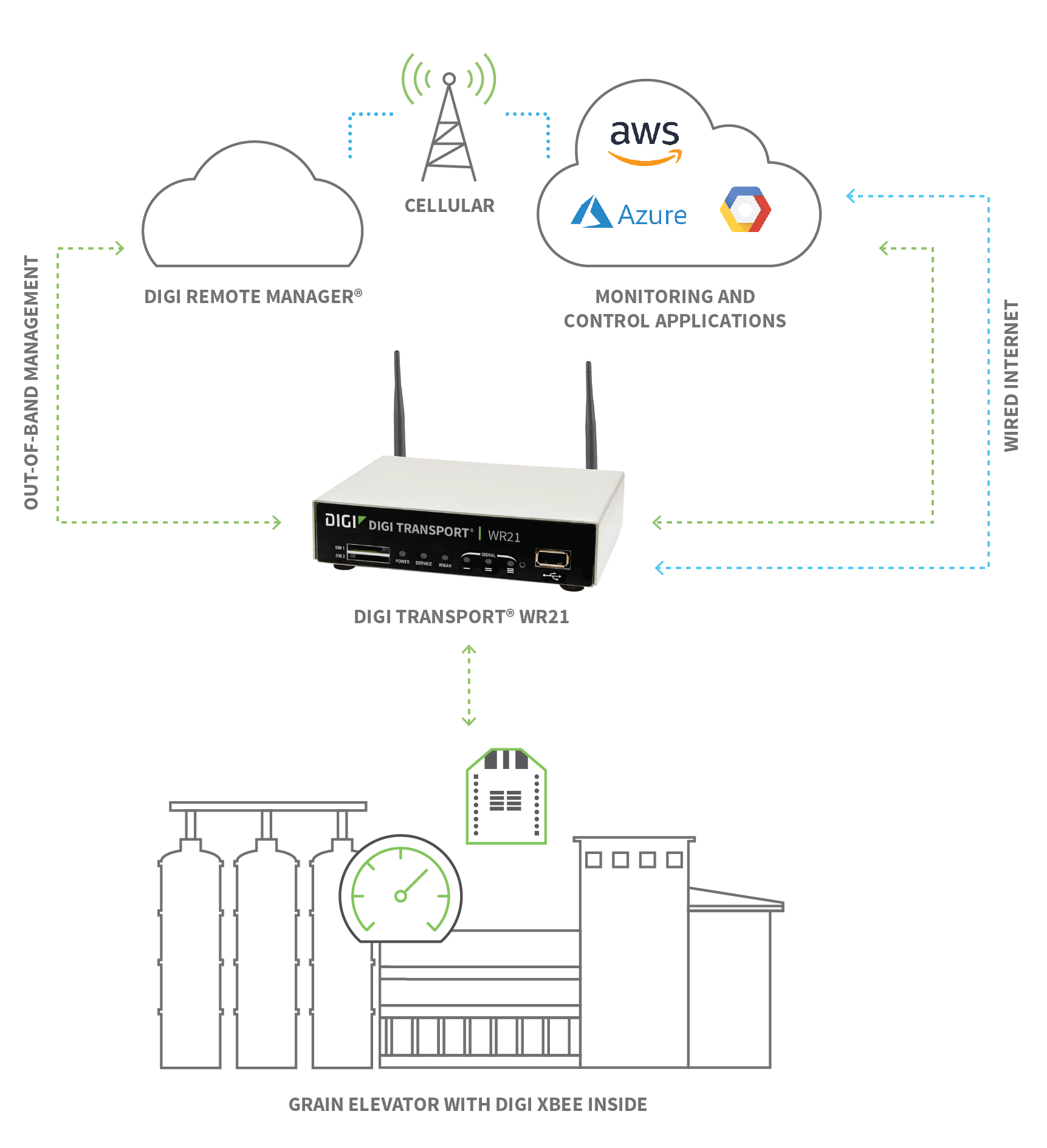
Remote Monitoring
Remote monitoring is at the center of many industrial applications, because it is traditionally inefficient, expensive and often challenging or risky to keep tabs on what is happening with equipment out in the field. Equipment that requires monitoring can be located at remote outposts, on the top of street lighting, inside a well or deep in a mine, making it not only impractical to regularly monitor that asset, but also expensive and risky.
The following are just some of the many examples of remote monitoring in industrial applications.
- Tank monitoring – oil and gas: Throwing rocks at a tank or using a stick to tap a tank to determine fluid levels have been common practices in the past that can be dramatically improved with IIoT applications. Tanks at production oil wells need to be monitored to ensure there is no overflow, which can result in hefty fines and cleanup costs. Monitoring onsite tanks with chemicals that are injected downhole to reduce pipeline corrosion are also an important part of daily operations. To reduce risk and optimize efficiencies, a company can install an automated tank monitoring solution that sends level readings as needed (such as by the minute, hourly or daily) to allow field managers to manage pickups or deliveries as well as preventive maintenance calls based on actual data and level readings. Taking this step also prevents the cost of sending personnel to each of the tanks on a rotation schedule, regardless of the tank levels. Instead they only send personnel when needed.
- Flow monitoring – agriculture: Center pivots in agriculture are a common way to distribute water across crop fields. Water goes through a pipe and is distributed through sprinklers as the center pivot moves slowly in a circle. A leak in a center pivot or any other irrigation line can cause major damage and cost thousands of dollars in repairs and lost resources. Remote monitoring of pressure and movement can help proactively identify issues on a irrigation pipeline. Plugged heads, leaks or even disconnected fittings can be sensed early and alarms sent to help farmers avoid issues, maintain crop growth, and limit capital spent on fixing problems.
- Chemical process monitoring – refineries: Remote management doesn’t have to be 100 miles. In many cases it may only be 100 feet, or a football field away. Monitoring at processing facilities has traditionally been done with wireline installations. One challenge is that cables are expensive to install and maintain. Another challenge is that wired systems can be subject to corrosive environments and other factors such as earthquakes and catastrophic weather events. A processing plant might have hundreds or thousands of sensors in place to gather data, for example to monitor a chemical batch, make sure it is under control and avoid spillage or explosions. Today, businesses such as these are turning to the Industrial Internet of Things to further monitor and automate processes, such as taking readings and recording them in a cloud-based system for analysis, reporting and alerts that can be accessed from mobile devices.
Wireless Tank Monitoring with 1844myfuels
"Digi has become a part of our whole solution. This is the first one that is truly wireless with a small footprint and works."
Read Story
Remote Monitoring Application Example
In this remote monitoring example, a radio module collects data from an industrial tank and routes it through an embedded processor to cloud-based applications for monitoring, alerts and adjustments.
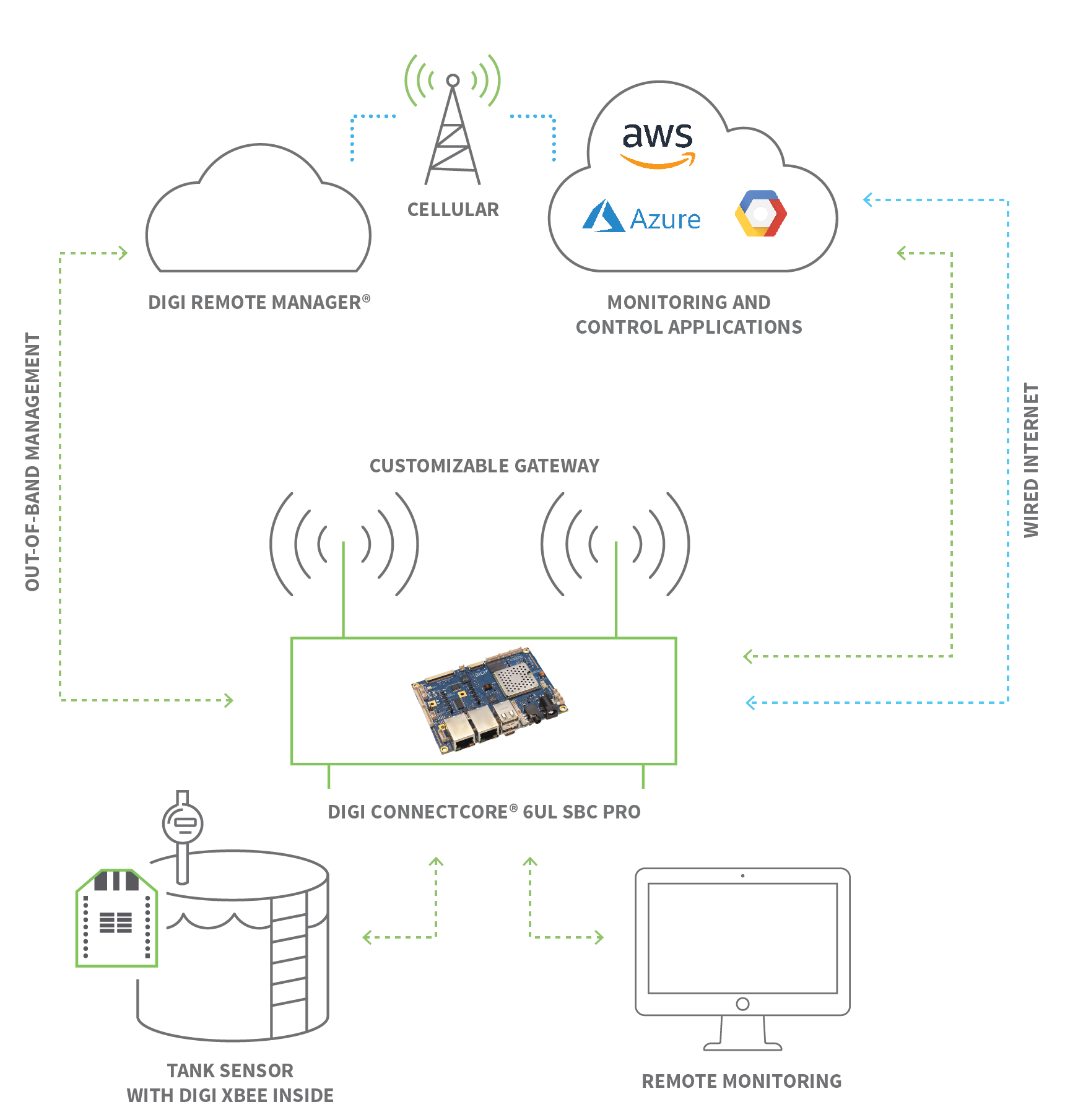
Process Automation
Automating processes that would otherwise require human intervention, truck rolls, or inefficient manual labor is another common reason for deploying connected applications in the industrial space. The range of use cases is vast, but the reasons for putting these Industrial Internet of Things processes in place again come down to a few key driving factors: efficiency, cost reduction and reduced risk.
Here are a few examples of automation in the IIoT.
- Smart Irrigation – The good old days of watering on a schedule just because you have water are slowly evaporating (pun intended). Today, farmers are adopting technology to monitor soil conditions and weather, among other factors, to determine when and where water is needed. Soil moisture sensors connected to wireless modules that relay sensor data to gateways and then the cloud allow farmers to monitor growing conditions. And automating the watering process based on moisture readings ensures water resources are used efficiently – where, when and for how long that watering is needed.
- Automatic modification – The energy sector today is turning toward automation to modify equipment behaviors based on conditions. For example, the wind often cools things down on a hot summer day. But too much wind can cause havoc in all sorts of environments, such as agriculture, wind mills and solar installations. When strong winds kick up in a solar field, weather stations can monitor when wind speeds can reach damaging thresholds. Wireless communication from a gateway can send commands to solar panels to move to a safety position that can help reduce or avoid damaging these high-cost assets.
- Frost fans – There’s nothing like an early frost to ruin your year-end harvest. Likewise a late frost in the spring might damage plants that are ready to bloom. Wireless sensor technology combined with giant fans on high value crops in orchards and vineyards allow farmers to monitor weather conditions so they can turn on fans to limit damage from early/late frost. It is a bit like having a heating and air conditioning system for your crops. However, these fans traditionally need to be manually turned on as unexpected frost temperatures arrive. This means farmers must make the rounds to each of the points where they have installed fans around their acreage, often in the middle of the night. An application that automates these processes can not only sense when temperatures are heading toward the frost range, but also trigger a process to start the fans. Meanwhile, the farmer can rest easy at night, and can see at a glance from a mobile device which fans have been turned on and if they are functioning properly.
Process Automation Application Example
In the following process automation example, soil sensors collect data, which is routed by a Digi XBee module with MicroPython to a Digi XBee Industrial Gateway, and then to cloud-based remote monitoring and control applications. One of these applications automatically launches processes, while another allows network managers or administrators to ensure all devices and processes are working as expected.launches
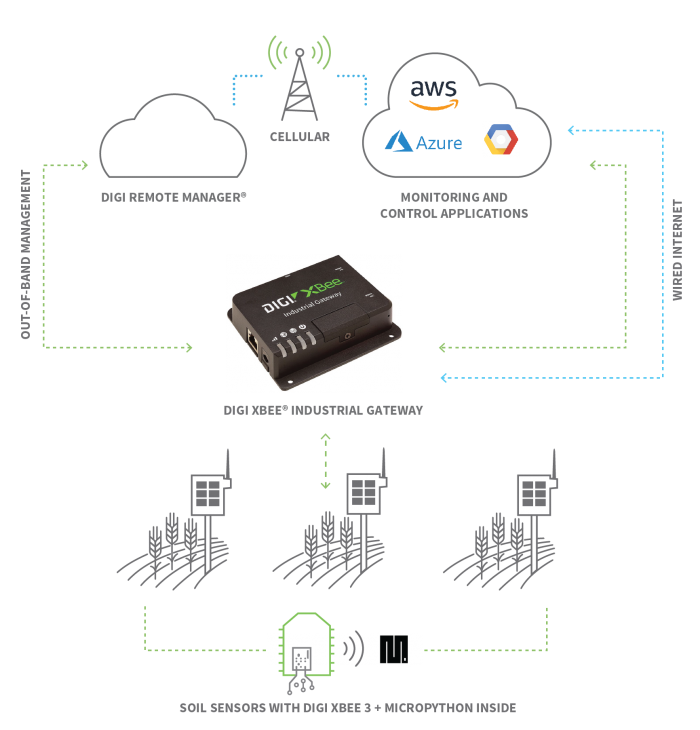
Important Considerations for Industrial IoT Applications
There are many things to consider when evaluating the right devices and setup for your Industrial IoT application. These include questions around the distance over which your IIoT devices will need to transmit data as well as the frequency of data submission, whether RF or cellular technology is appropriate for your application, and many other decisions that impact the overall planning, deployment, scalability and management of your project and that ultimately affect your total cost of ownership.
We will cover a few of the things to consider as you prepare to design, build out and deploy your project. If you have questions or are ready to evaluate solutions, Digi team members can partner with you to perform a full evaluation of your application needs. And Digi design and engineering teams are also available for any level of support in developing your IIoT appliation. Contact us to start that conversation.
Industrial Devices vs. Prototyping Tools:
A critical step for Industrial IoT applications – and in fact any professional product that will face environmental challenges such as fluctuating temperatures or vibration – is to find the right product for the job. If you develop a product for an application such as a city bicycle ride share service, for example, the application may not technically be considered an industrial application, but its requirements are similar as it will need to be able to handle jarring movement, temperature changes and moisture. Some types of devices can handle challenging environmental factors, and some are less suitable. So it is critical to evaluate the robustness of a product and whether it is designed for the intended application.
There are many low-cost modules that are excellent for rapid prototyping and for student projects, such as Raspberry Pi and Arduino. The attractive cost is a good reason to use these products in initial phases. But you will want an industrial-rated product designed for long-term viability in demanding environments when seeking products that are suitable for IIoT applications.
Some of the factors to evaluate in a product include:
- Manufacturing quality control
- Long-term availability and stability of the product
- Tested temperature ranges
- Design flexibility and programmability
- Availability of supporting tools and code libraries
- Ability to proactively update firmware, particularly when your deployment scales beyond a few devices
- Certifications in the regions where your application will be deployed.
Starting with a prototyping tool is a great way to prove a concept; but when you are ready to go the field with deployed devices, be sure to select industrial rated devices.
Remote Management Strategy
Traditional maintenance methods of sending a truck out to the field to monitor or manage equipment quickly becomes impractical and costly when you have dozens, or hundreds, or even thousands of devices to maintain. Just like your cell phone, which has firmware upgrades that are pushed out it regularly, devices have firmware updates and security patches that must be sent to each of the devices in your IIoT network to keep those devices up-to-date and secure. A remote management solution allows you to send bug fixes and feature enhancements to all of your devices in the field, regardless of the size of your network.
To implement a remote management strategy, look for a solution that will enable you to perform remote firmware upgrades, device connectivity, and remote diagnostics from anywhere, using a smart device. For example, Digi Remote Manager® is a cloud-based solution that provides these capabilities and more, enabling you to set alerts for a range of conditions, download files, and automatically monitor device configurations and reset them to the correct version in the event of tampering.
Putting a remote management system in place is highly economical compared with the cost of sending a bucket truck to manually upgrade the firmware on a device mounted on a sign or street light, and enables your network manager to keep tabs on all of devices, regardless of how many devices you have in your network or where they are in the world.
Conclusion
The evaluation and decision making that go into the development and deployment of an IIoT application can be daunting. Digi can support your quest to identify the right solution for your needs at any point along the way, from initial project scoping to complete engineering and certification services.
Whether you want to demonstrate the ROI of a new product or need to meet a strict deadline for compliance or market pressures, Digi can partner with you to achieve those goals. Time to market can be especially critical when there is a short-lived window of opportunity to get ahead of competition.
Working with a company that has proven professional consulting and engineering support not only gives you the assurance that you can meet deadlines and launch dates, but also helps you complete design reviews and get certification assistance when your resources stretched thin. Contact us to evaluate options.