Every enterprise needs to run more efficiently, whether to combat the cost of doing business, identify and prevent potential equipment failures before they happen, or buffer against a talent shortage. Industrial remote monitoring can help. With remote monitoring, your industrial operation can have eyes and ears at the most remote locations, without having to send personnel to those sites for every issue, large or small.
Improvements in operational efficiency. Cost savings. Improved safety. Enhanced process quality. Not to mention the fact that fewer truck rolls means better environmental stewardship. These are just a few of the driving factors behind the move to industrial remote monitoring in a vast number of industrial operations. In this blog post, we cover the different types of monitoring, and how they support a more robust enterprise with better outcomes.
What Is Industrial Remote Monitoring
Knowing that a machine in your manufacturing line is likely to fail can reduce downtime and save costs and labor. Today, industrial remote monitoring can provide these kinds of critical insights across factory floors, equipment rooms, mining operations, utilities, water and wastewater operations, digital oil fields, and more. By integrating your industrial remote monitoring systems into an integrated system connected to a cloud-based software platform, you can gain mission-critical visibility, receive alerts that indicate anomalies, automatically launch service tickets, and take other measures to keep operations on schedule and eliminate downtime.
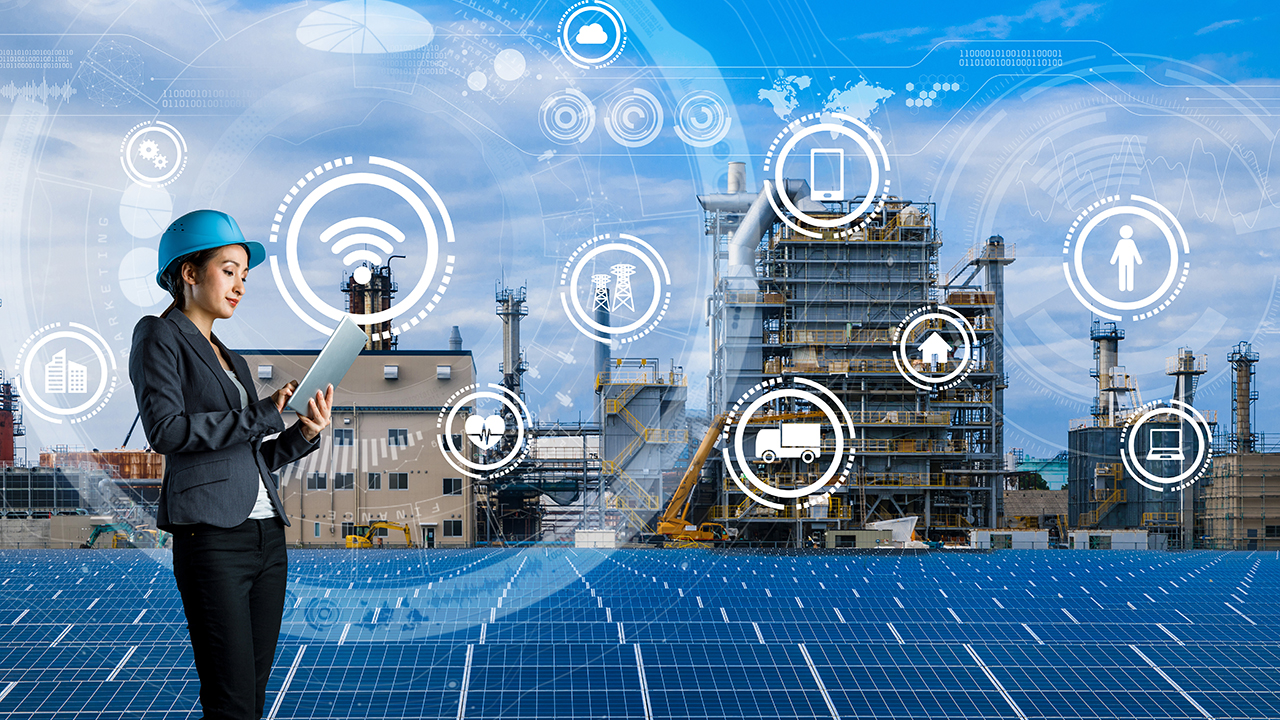
Why Does Industrial Remote Monitoring Matter?
Safety and cost savings are key benefits of industrial remote monitoring. For example, Journeo of the U.K. developed an end-to-end solution that delivers real-time information on vehicles, systems, and IoT sensors across the entire transit network — not only improving passenger safety but also providing visibility into hazards and CCTV footage in the event of an incident for analysis.
An industrial remote monitoring system provides many ways to reduce costs. For example, alerts can warn of equipment failures and errant environmental emissions. Remote monitoring helps operators improve safety, prevent costly unscheduled downtime and avoid fines.
Key Reasons Industrial Remote Monitoring Matters
- Improve efficiency — Leverage offsite expertise, automate device updates and gain data-driven insights
- Reduce costs — Reduce service calls and the related costs and environmental impact of fuel burning vehicles
- Keep your teams safe — Industrial monitoring can replace manual inspections in hazardous areas
Types of Industrial Remote Monitoring
Manufacturing often operates on thin margins. Every efficiency, safety and cost improvement solution matters. That’s why manufacturing has many remote monitoring use cases. But industrial remote monitoring supports critical insights, automation and operational improvements in every industrial field.
Other industries that benefit from industrial remote monitoring include (but are not limited to) agriculture, mining, water and wastewater management, rail and other mass transportation systems, the oil and gas industry, power generation plants and even construction operations.
Download Digi’s Industrial IoT Automation white paper.
Manufacturing Processes
Manufacturers improve safety, reduce costs and gain real-time insights through industrial remote monitoring. By wirelessly connecting production lines to cloud-based software, manufacturers get real-time information about their manufacturing line processes. But that is just the start. Manufacturing monitoring systems provide managers with other benefits, too. These include predictive maintenance, improved product quality, increased machine uptime and the ability to deploy automatic software and security updates.
Predictive Maintenance
Maintenance monitoring is an important part of any industrial process. Real-time sensor data from machines gets displayed on a digital dashboard. This helps operators maximize uptime and cut maintenance costs. OTIS Elevator, for example, uses advanced software tools to predict equipment issues before they happen. As a result, managers can schedule maintenance in advance, instead of reacting to unplanned failures.
Emissions Monitoring
Industrial processes that can release gases and chemicals into the atmosphere must be carefully monitored to ensure they do not negatively impact the environment. Any industry with gas emissions must meet stringent regulatory requirements. Remote monitoring solutions use sensors to measure emissions. They supply information in real-time to help industrial operators mitigate environmental impact.
SCADA Configuration and Data Recovery
SCADA (supervisory control and data acquisition) systems include both hardware and software-based components. These systems gather real-time data from industrial processes to control machines and automated systems. Increased interest in renewable energy sources and increased water demand are driving industrial equipment monitoring. Many industries use SCADA systems, including all types of manufacturing, utilities, oil and gas refining operations, power generation and telecommunications infrastructure.
Learn more about industrial remote monitoring and how it can benefit your organization.
Business Benefits of Industrial Remote Monitoring
Every industry seeks a balance between improving operational efficiency and better quality. An industrial monitoring system that scales with your organization as your needs change can do just that.
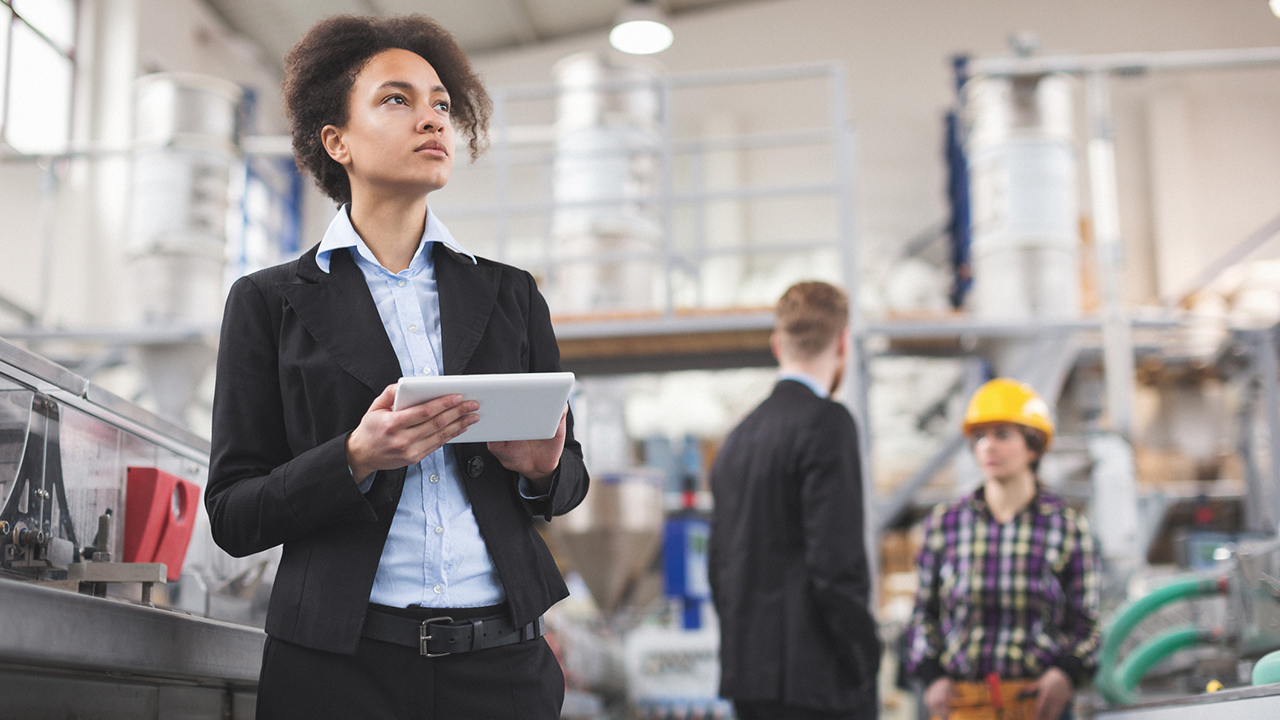
Maximize ROI
Ultimately, every investment decision comes down to understanding the return. How long will it take to realize a return on an investment? Is the investment going to benefit my customers? What happens if I decide not to make the investment? These are some of the questions businesses ask when evaluating an investment in new technology.
As industrial enterprises consider investing in an industrial remote monitoring system, they often find that there are multiple cost-saving and environmental benefits.
When deciding on an industrial remote monitoring investment, consider how these systems can improve your ROI.
- Lower operating costs — The cost of manually managing IoT devices without a system can quickly overtake the cost of a remote equipment monitoring system
- Scale without adding staff — Whether you are short-staffed or budget-constrained, industrial remote monitoring automation can reduce the need for hiring extra staff
- Prove regulatory compliance to avoid fines — Monitoring systems collect and manage data to prove that your systems follow regulatory requirements
Oversee Quality
The quality of your industrial processes directly affects your operations and the quality of your output, since everything from air temperature, to machine health and cybersecurity can affect your processes. With industrial remote process monitoring, hardware and software work together to track production. Operators receive alerts when something changes. If industrial processes form the core of your business, you simply cannot afford to compromise on quality.
Three key capabilities of industrial remote monitoring that can benefit your business:
- Proactively manage processes automatically — Receive alerts when monitored metrics change
- Identify root causes quickly — Identify quality issues before they impact production
- Predict breakdowns before they occur — Analyze quality data over time to predict future breakdowns
Optimize Performance
How do you currently optimize the performance of your systems? With industrial remote monitoring, sensors connected to your machines share large volumes of real-time data. Machine operators enjoy the convenience of getting performance insights remotely from any device. Remote monitoring also helps maximize uptime while minimizing maintenance costs. For your operations, proactive performance monitoring can reduce downtime and lost productivity.
Optimizing performance through an industrial remote monitoring system means your operators can:
- Control processes from anywhere
- Get real-time insights into the health of your operations
- Use predictive maintenance alerts to proactively schedule repairs
Ensure Safety
Your workforce is the lifeblood of your organization. Technology helps people do their jobs better, gain deeper insights and even find opportunities to add extra value. But perhaps the most important role of technology in the industrial space is to ensure safety.
Industrial remote monitoring plays a large role in improving operational safety, by enabling industrial outfits to gain visibility into their systems and processes anywhere — whether those processes are occurring deep inside a mine, at the top of a light pole, at a remote wellhead, or in an underground water system. Whether the site itself presents hazards based on location, hazardous substances, or conditions, gaining insights from those systems via an IoT-based monitoring system can protect your personnel.
How Industrial Remote Monitoring Systems Ensure Safety
- Reduces risk by automating routine maintenance tasks — Automating inspections in hazardous locations reduces injury risk
- Free your team to address maintenance proactively — Urgent emergency repairs can lead to injury when workers don’t have time to plan
- Safety benefits offset the investment — Investing in monitoring systems improves worker safety—it is an investment in your people
Centralized Management of Remote Industrial IoT Devices
Major Oil and Gas Operation Monitors Edge IoT Devices with Digi Remote Manager.
Download PDF
Industrial Remote Monitoring Use Case Examples
Industrial remote monitoring uses hardware and software tools to manage industrial processes. These tools create efficiencies and insights not possible with manual processes.
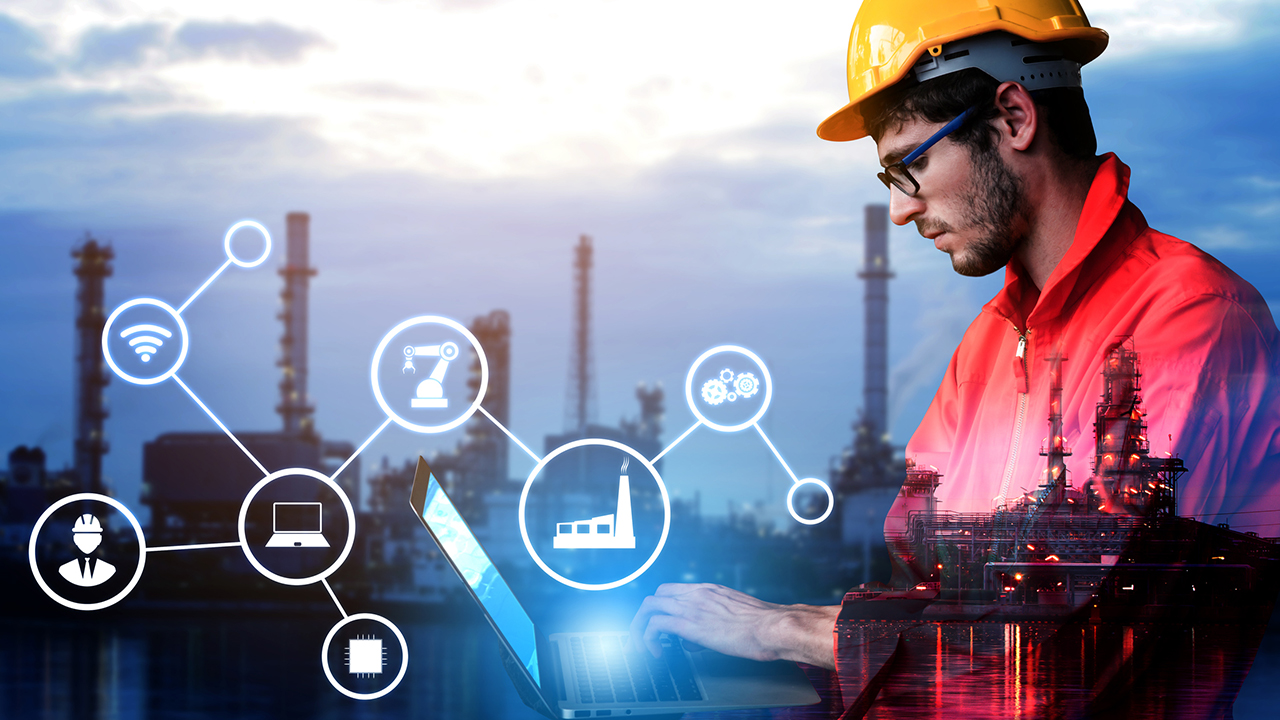
Precision Agriculture
Precision agriculture involves observing, measuring and responding to changes in crops and growing conditions. Jain Irrigation offers one example of precision agriculture remote monitoring. Jain Irrigation is a world leading irrigation solutions company. Jain understands that traditional residential irrigation methods can waste as much as 50 percent of the water they spray.
Jain’s solutions automate and optimize watering and fertilizing strategies. Their solution results in reduced labor and energy costs and maximized yields. But they needed an affordable cloud communications solution they could trust. That’s why Jain partnered with Digi and the Digi XBee® 3 Cellular LTE series modems.
Find out more about remote monitoring in precision agriculture.
Industrial Remote Monitoring Applications in Precision Agriculture
Environmental Monitoring
Environmental monitoring uses a distributed sensor system, wireless connectivity, edge computing and software tools to check and manage environmental conditions. It aims to prevent events harmful to the environment. Environmental conditions also include the health of machines and equipment. Whether its monitoring air, soil or water, remote environmental monitoring solutions using new wireless technology provides a range of benefits.
Learn more about environmental monitoring
Common Environmental Monitoring Applications
- Pollution monitoring — Observe, measure, and manage contamination in water, air and soil
- Leak detection — Oil and gas companies use leak detection on pipelines
- Wastewater and groundwater monitoring — Record and measure public health impacts, water availability, agricultural yields and more
Manufacturing Automation
Manufacturers use integrated connectivity on the factory floor to track and discover production issues. A centralized cloud system also allows managers to remotely monitor the equipment and send software and firmware updates. Operations managers using these tools can reduce maintenance costs while also increasing productivity.
Learn more about manufacturing automation.
Industrial Remote Monitoring in Manufacturing Scenarios
- Real-time monitoring to reduce downtime
- Reduce maintenance costs through remote asset visibility
- Improve worker safety by incorporating wireless systems and sensors in dangerous work environments
Asset and Inventory Monitoring
Tracking assets and inventory remotely with IoT technology is a game changer. Asset tracking helps companies check on high-value equipment in real time. Any industry that manages lots of equipment can track inventory location and condition. In real time, managers can gain perspectives on equipment health, asset loss or poor operator handling.
Learn more about asset and inventory monitoring.
Use Cases for Asset and Inventory Monitoring
- Monitor valuable assets with IoT and management software
- Remotely conduct inspections that replace or reduce on-site visits
- Use Radio Frequency Identification (RFID) tags to communicate information about inventory, including location data
Learn how you can configure, deploy and manage deploy and manage remote assets securely with Digi Remote Manager®.
Explore Digi’s Industrial Remote Monitoring Solutions
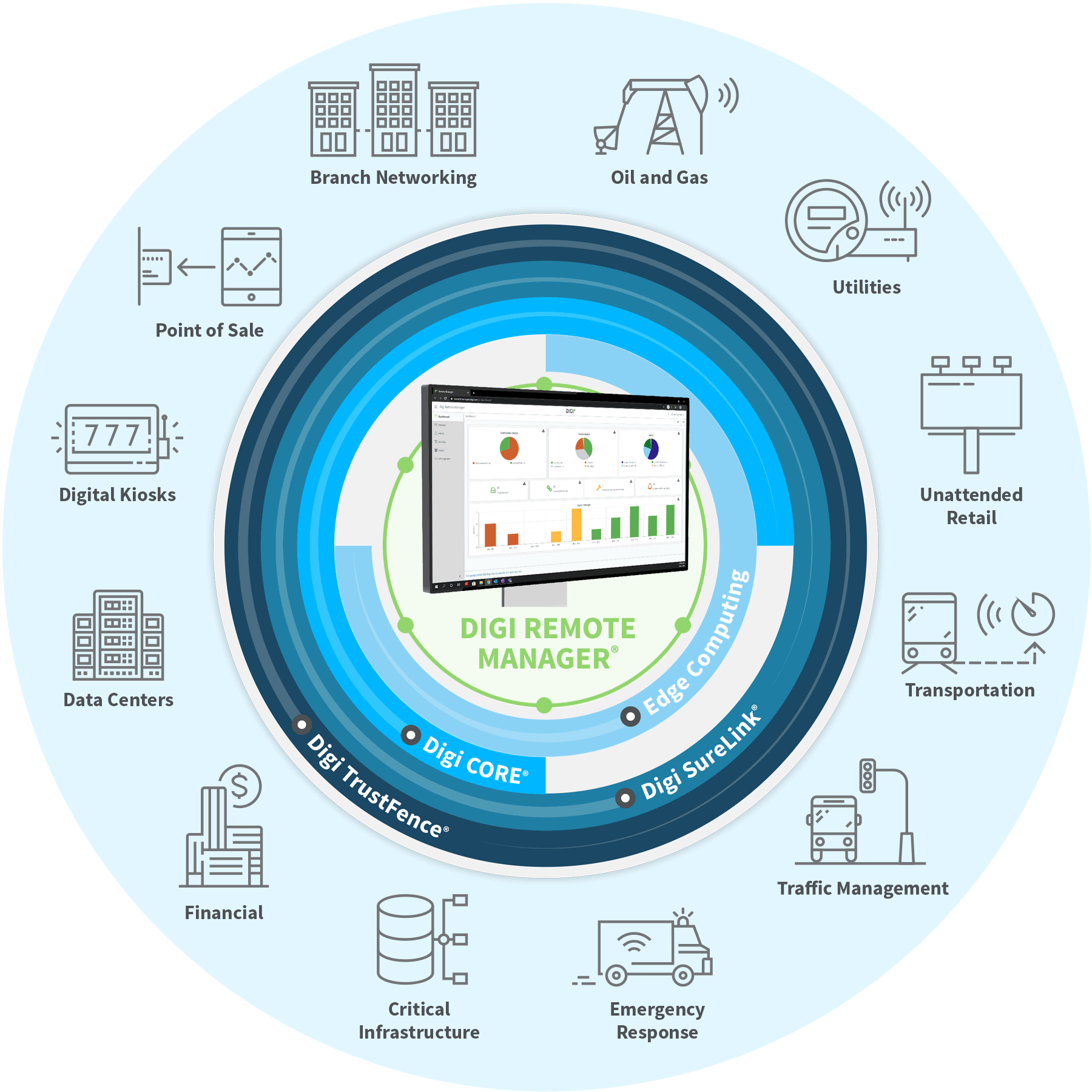
In this blog post, we've shared the excellent benefits and use cases for various types of industrial remote monitoring. As your organization deals with economic and talent pressures, industrial remote monitoring can help. In fact, incorporating a secure, end-to-end solution can transform your business — for your employees, your customers, your environmental impact, and your bottom line.
Digi has over 35 years of experience designing and implementing mission-critical connectivity. We have the expertise and scalable remote cellular connectivity solutions, embedded communications solutions and infrastructure management solutions to help companies successfully navigate industrial communications challenges.
Next Steps